Why do some gloves feel & perform better than others?
Gloves fibres & differences explained.
It’s all about the Colours
For some time now it has been recognised that high performance cut resistance gloves in solid Hi-Vis fibres would be a good idea, so why doesn’t everyone manufacture Hi-Vis solid coloured gloves?
Most of the industry cuts corners and adds a simple dip colour on the palm. But that does not solve the problem because you can’t see the palm of the glove when you are using it!
There is a reason why many manufacturers struggle with it. In basic terms, Cut 1 gloves have a relatively low density so colours and dyes can absorb into the fibres relatively easily, but once Cut 3 and higher fibres are used it becomes very hard to penetrate the fibres, (hence why they are rated for higher protection).
Therefore, getting bright Hi-Vis solid colours in these fibres have been very difficult if not impossible with conventional methods, but The Glove Company has successfully done just that, with our KOMODO® Vigilant range of gloves.
Through a unique, ground-breaking process, KOMODO® Vigilant gloves have been able to match solid Hi-Vis colours with cut ratings.
How To Manage Risks & Hazards
As a manufacturer, it has always been our goal to minimise any confusion about which glove to use and where to use it. This was our goal behind the Vigilant glove range. We wanted to integrate simple visual signals with a task or a hazard.
There are 3 KOMODO Vigilant Gloves; Green – for low risk, Yellow – for medium risk, and Red – for high risk. To find out more information about managing hazards, click here.
Your Standard Operating Procedure (SOP) decided that a task is low risk; therefore, everyone working on that task needs a Green Glove. Alternatively, if the task is a high risk, then everyone working on it needs to be wearing red gloves. The key to the KOMODO Vigilant gloves success is the pure simpleness of them.
Anyone can understand the visual hazard cues. There is no language or technical jargon barrier to workplace safety.
No more which glove do I use confusion and what do all these numbers on the glove mean? Just check the SOP and go, furthermore supervisors can quickly see at a distance that the SOP is being carried out correctly.
Your Fibres Matter
The key to understanding the differences between gloves is knowing the 1, stitch count, 2 High-Performance Polyamide (HPPA) and 3 Twists per Meter (TPM).
1. Stitch Count: the more stitches per cubic meter, the better the comfort and protection the glove will provide.
2. HPPA: Is the backbone of cut resistance, with Nylon and Spandex added to alter the physical properties of elasticity and abrasion.
3. TPM: Is the important measure of the quality of the finished fibre, simply put the more twists on and around the HPPA the longer lasting and higher protection the glove will provide the user.
KOMODO Vigilant gloves have some of the highest stitch counts per cubic meter of any glove available. Additionally, the TPM on KOMODO Vigilant gloves is one of the highest in the industry at 2860 TPM, with standard gloves being as low as 850 TPM.
These features are hard to see but are easy to feel from the moment you put the glove on and are the answer to the questions; why do these gloves feel so much better than all the others?
Keeping Your Cool
When you manufacture a quality glove with a high stitch count, the glove will have the additional benefit of keeping you cooler in summer and warmer in winter.
Our specially engineered fibres are designed to pull sweat and moisture away from the hand to the outer surface of the glove liner.
The liner within the glove is also designed to help circulate air between the skin and the liner for faster evaporation. The wicking performance fabric pushes excess moisture away from the skin.
It works by absorbing and spreading moisture out across the fabric to enhance the evaporative drying rate.
Creating high-performance gloves that are soft, breathable and moisture wicking.
Don’t Just Take Our Word For It
Testing: Is crucial in the safety industry.
Always ensure that the gloves you decide on are independently third-party tested and certified.
Unless the results have come from an independent thirty party accredited test facility, then you are just taking someone’s word for it.
It is also advised that the facility is based in a country where standards enforcement is strong.
The Glove Company gloves have been independently third-party tested in Australia under AS/NZS 21.3:2005 / EN388 in conjunction with Vic Labs who have in turn been independently tested and accredited that their test results are of the highest standard.
High-Quality Gloves
Get the blend of HPPA, Nylon and Spandex just right with a high TPM (Twists Per Metre) count and coat it with a tough but flexible outer of high chemical resistance PU, and the result is a sublime glove featuring both comfort and performance.
When you add a practical black coating colour, that helps extend the life of the gloves. The gloves will last the optimum amount of time, saving you costs.
Now that’s a handy, Smart Glove
We even added the unique benefit of touch screen compatibility across the range from Cut 1 to Cut 5.
Even when operating touch screens devices, you can use the unique KOMODO® Vigilant smart glove technology with Smartphones to Tablets, GPS, Control panels, laptop screens, navigation systems and a lot more.
Naturally, there is a sharp increase in both productivity and safety as a result of using a KOMODO® Vigilant Smart glove. Not having to remove the gloves and re-don many times throughout the day is a massive benefit to users and encourages them to adhere to SOPs.
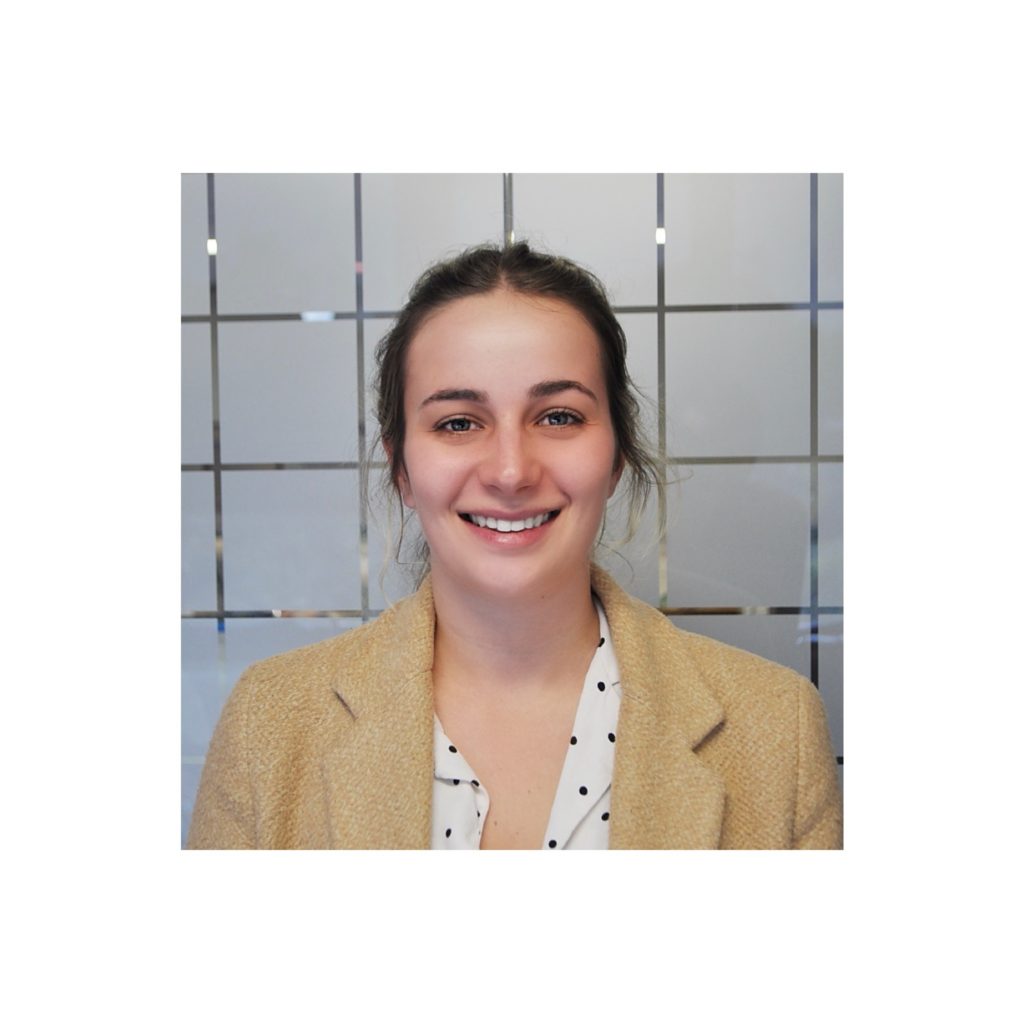
Written by Yvette Staples
Marketing & Communications Manager – with over 5 years experience in the health & safety industry.